Porosity in Welding: Identifying Common Issues and Implementing Best Practices for Avoidance
Porosity in welding is a prevalent issue that typically goes unnoticed till it creates significant troubles with the integrity of welds. In this conversation, we will certainly explore the essential aspects adding to porosity development, examine its destructive effects on weld efficiency, and discuss the ideal methods that can be embraced to lessen porosity event in welding processes.
Common Sources Of Porosity
Making use of unclean or damp filler products can present pollutants into the weld, adding to porosity problems. To mitigate these typical reasons of porosity, complete cleansing of base steels, appropriate protecting gas choice, and adherence to optimal welding criteria are necessary methods in achieving high-grade, porosity-free welds.
Influence of Porosity on Weld Top Quality

The presence of porosity in welding can considerably endanger the architectural integrity and mechanical residential properties of bonded joints. Porosity develops spaces within the weld metal, deteriorating its overall toughness and load-bearing capacity.
Among the primary effects of porosity is a reduction in the weld's ductility and toughness. Welds with high porosity levels have a tendency to display reduced influence strength and reduced capability to warp plastically prior to fracturing. This can be specifically worrying in applications where the bonded parts are subjected to dynamic or cyclic loading conditions. Furthermore, porosity can restrain the weld's capacity to effectively transmit forces, bring about premature weld failure and prospective security dangers in essential frameworks.
Finest Practices for Porosity Prevention
To improve the architectural stability and quality of welded joints, what details measures can be implemented to decrease the incident of porosity throughout the welding process? Making use of the appropriate welding method for the specific material being bonded, such as readjusting the welding angle and gun position, can even more protect against porosity. Regular evaluation of welds and instant removal of any kind of concerns identified during the welding procedure are important methods to protect against porosity and produce top notch welds.
Importance of Proper Welding Strategies
Carrying out proper welding techniques is critical in useful content guaranteeing the architectural stability and quality of welded joints, building on the foundation of effective porosity avoidance steps. Welding techniques straight affect the total strength and durability of the bonded framework. One essential aspect of correct welding strategies is keeping the appropriate warmth input. Extreme heat can bring about raised porosity because of the entrapment of gases in the weld pool. Alternatively, inadequate warmth may cause incomplete blend, creating prospective weak factors in the joint. Additionally, utilizing the proper welding criteria, such as voltage, existing, and take a trip speed, is critical for achieving audio welds with minimal porosity.
Moreover, the selection of welding procedure, whether it be MIG, TIG, or stick welding, ought to line up with the specific demands of the task to make certain optimum results. Proper cleaning and prep work of the base metal, along with selecting the ideal filler product, are likewise vital parts of efficient welding techniques. By adhering to these finest methods, welders can minimize the risk of porosity formation and produce top notch, structurally audio welds.
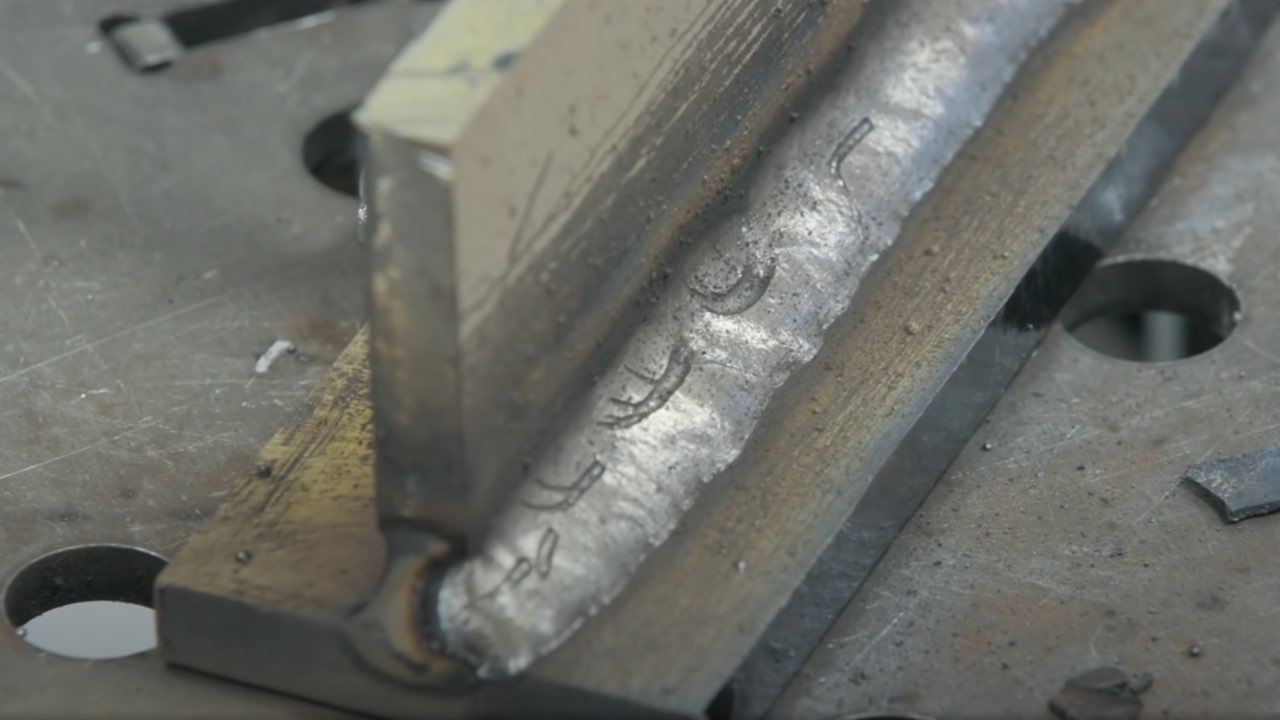
Evaluating and Top Quality Control Steps
Quality assurance measures play a vital role in verifying the stability and integrity of welded joints. Evaluating treatments are essential to spot and stop porosity in welding, ensuring the strength and toughness of the end product. Non-destructive testing techniques such as ultrasonic testing, radiographic testing, and aesthetic assessment are generally used to identify potential problems like porosity. These methods enable for the evaluation of weld top quality without endangering the honesty of the joint. What is Porosity.
Post-weld examinations, on the various other hand, examine the final weld for any defects, consisting of porosity, and validate that it meets specified criteria. Implementing More about the author an extensive top quality control plan that includes complete screening procedures and evaluations is extremely important to reducing porosity problems and making sure the total high quality of bonded joints.
Final Thought
Finally, porosity in welding can be a common concern that impacts Full Report the top quality of welds. By determining the common reasons of porosity and executing best techniques for prevention, such as correct welding techniques and testing procedures, welders can make sure high top quality and reliable welds. It is important to prioritize prevention techniques to lessen the incident of porosity and preserve the stability of bonded structures.